A logisztika területén az utóbbi időszakban jelentős változások zajlottak le. Ez a szegmens volt képes arra, hogy az elé gördülő akadályokat a lehető leghatékonyabban, új fejlesztések és technológiák integrálásával oldja fel. Horváth Zoltánnal, a Jungheinrich Hungária Kft. ügyvezető igazgatójával beszélgettünk az ágazat fejlődéséről.
Az elmúlt időszakban több alkalommal is jelentős megrázkódtatás érte a piacot, amelyben a logisztikai terület különösen értintett volt, és azonnal reagálnia kellett a változásokra. Milyen trendek figyelhetők meg ma a hatékony raktárüzemeltetés terén?
Az elmúlt öt év számos olyan kihívást hozott magával, amellyel korábban még nem találkoztunk. Ilyen volt például a Covid-járvány, a háború és annak következménye, az energiaválság, amely felborította az addig jól bevált működési folyamatokat és az ellátási láncokat. Mindez felgyorsította a környezettudatos, fenntartható megoldások irányába mutató folyamatokat.
Világszinten a logisztika és a szállítás felelős a szén-dioxid-kibocsátás csaknem 23%-ért, és ennek negyedét az intralogisztika teszi ki. Ezért nem mindegy, hogy milyen meghajtású anyagmozgatógépek üzemelnek a gyárakban, raktárakban. Mindezen tényezőket tekintve tehát alaposan mérlegelni kell, hogy milyen gépet választunk egy beszerzési folyamat során.
A szén-dioxid-kibocsátás csökkentése és a hatékonyság növelése alapvető elvárás a mai kor intralogisztikai fejlesztéseiben. A Jungheinrichnél mindig is odafigyeltünk arra, hogy a termékeink hatékonyak legyenek. Ma már számos anyagmozgató gépet gyártunk, amelyek alacsony szén-dioxid-kibocsátással üzemelnek. Vállalásaink között pedig az szerepel, hogy 2040-re a vállalat szén-dioxid-semleges legyen. Tudjuk, hogy az általunk választott, jövő felé vezető út költségesebb, de mi készek vagyunk ezt az árat megfizetni a fenntarthatóság érdekében.
Mit tart különösen kiemelkedő teljesítménynek ezen a téren?
Jelenleg a lítiumion-technológiához kötődik a legnagyobb CO2-megtakarítás, amely technológia meghonosításában Magyarországon úttörő szerepet vállaltunk. Igaz ugyan, hogy a lítiumion-akkumulátorral működő targoncák beszerzési értéke magasabb, mint a más technológiát használó gépeké, de TCO (total cost of ownership) szemléletben gondolkodva ez egy gyorsan megtérülő beruházás lehet, ha minden szempontot figyelembe vesszük.
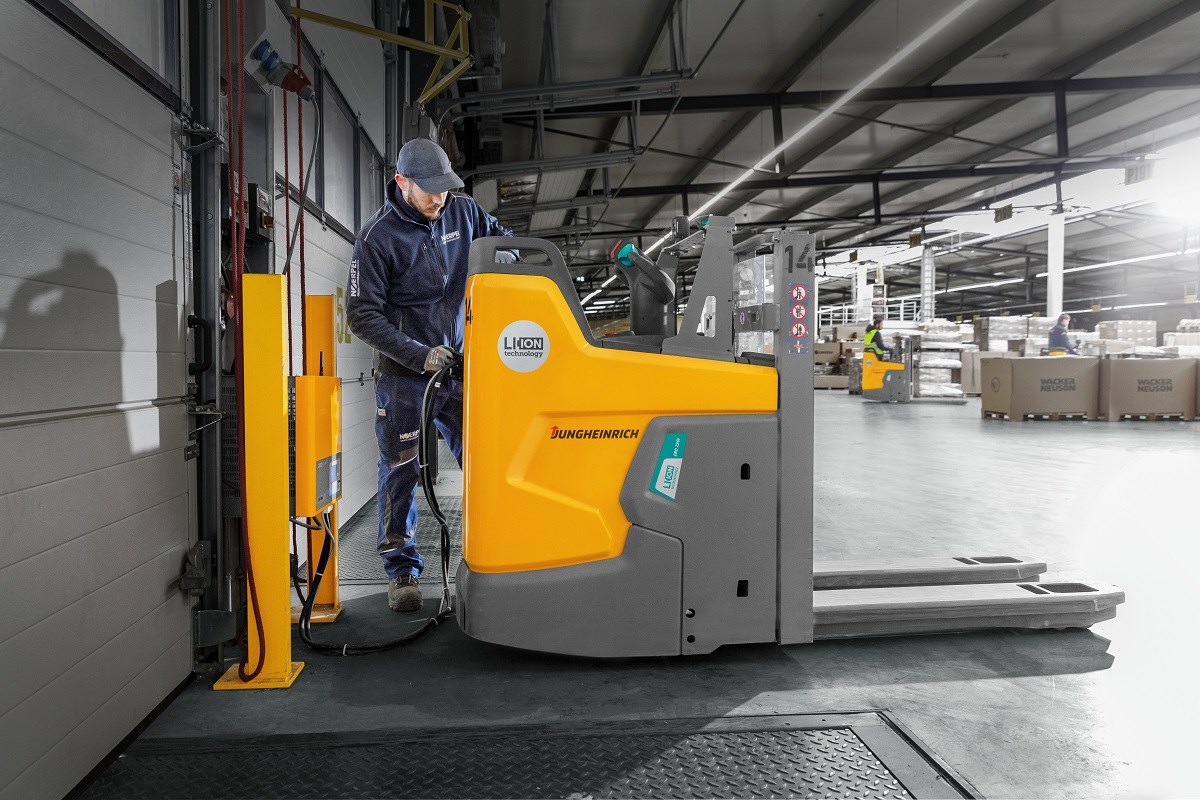
Lítiumion akkumulátorral szerelt targoncák töltése.
© Jungheinrich Hungária Kft.
A fenntarthatóság a folyamatok optimalizálásáról szól, ami költségoptimalizálást egyaránt jelent. Egy értékláncon belül számos elem optimalizálható, de lényeges kérdés a munkaerő és a minőség is, valamint az árubiztonság – hogy csak néhányat említsek –, és mindezekre a fenntarthatóság kapcsán teljes körű megoldást tudunk adni az automatizálással.
Mekkora nagyságrendű hatékonyságnövekedést lehet elérni ezzel és mik ennek a feltételei?
Meggyőződésünk, hogy a lítiumion-technológia az, amely korunk igényeit ki tudja szolgálni, hiszen jelenleg ennek a technológiának nincs olyan alternatívája, amely ipari méretekben alkalmazható. Úgy véljük, a lítiumion-akkumulátorral szerelt gépek aránya 2025-re akár a 75%-ot is elérheti.
Számos szempontot érdemes figyelembe venni, melyekkel hatékonyabban üzemeltethetők a berendezések. Fontos a töltőberendezések számának meghatározása, amely befolyásolja az elektromos hálózat infrastrukturális beruházási igényét. De lényeges a töltésmenedzsment is, amely előre meghatározott rendszerelemek alapján optimalizálni képes az energiafelvételt, és ezzel egy áramcsúcs, valamint a kapcsolódó költségek is csökkenthetők.
Egy jól megalkotott rendszer hatékonyan használja fel az energiát. Emellett figyelmet kell fordítani a megfelelő akkumulátor és töltő kiválasztására is egy adott anyagmozgató gép kapcsán, mert ennek révén az energiaveszteség egy része megtakarítható – természetesen a lítiumion-akkumulátorok alkalmazásával. Ezek rendkívül gyorsan és rugalmasan, illetve köztes időkben is tölthetők. Hosszabb az élettartamuk, mint a hagyományos ólomsavas akkumulátoroké, és karbantartásmentesek, emellett nincs szükség költséges infrastruktúrára.
Ha a hazai piacot nézzük: itthon mennyire népszerű vagy elterjedt a különböző raktári folyamatok automatizálása?
Az elmúlt pár évben megélénkült az érdeklődés az automatizálás iránt, hiszen nincs elegendő mennyiségű és megfelelően képzett munkaerő. Ugyanakkor ezek a technológiák részben az elmúlt évek geopolitikai tendenciái, részben a Covid-hullámok, de az árfolyamingadozás miatt sem lettek „olcsóbbak”. Bizonyos alkotóelemeik szállítási határideje akár az 1 évet is meghaladhatja, illetve az előbb említetteknek köszönhetően a beszerzési áruk is emelkedett. Az említett negatív tendenciák ellenére dinamikus fejlődés jellemző a magyar piacra is: mára már mindennapos az, hogy a cégek ezekben a technológiákban gondolkodnak, legyen szó beruházásról vagy üzemeltetésről. Egy kis érdekesség: a Jungheinrichnél az automatizálás egyébként több évtizedes múltra vezethető vissza. A legelső, induktív pályán közlekedő AGV-t (automated guided vehicle) 1962-ben mutatta be a vállalat, és ma már ehhez képest a harmadik generációs gépeket állítjuk üzembe, amelyeknél nem szükséges már semmilyen emberi beavatkozás.
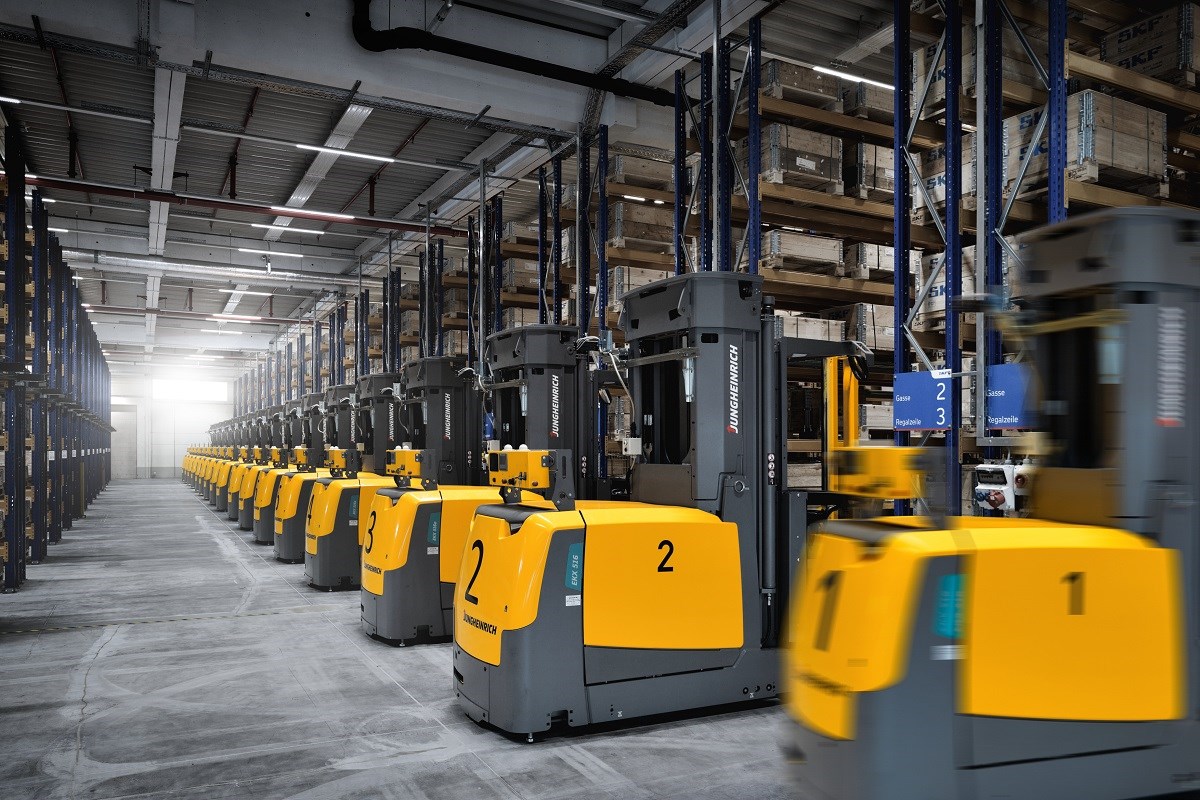
Az önvezető targoncák, mobil robotok biztonságosabbá és hatékonyabbá teszik a raktárak üzemeltetését.
© Jungheinrich Hunária Kft.
Az automatizációs folyamatokat két oldalról lehet megközelíteni. Egyrészt a technológiai, másrészt felhasználhatósági oldalról. A technológiát tekintve léteznek az önmaguktól működő rendszerek – felrakógépes magasraktári megoldások –, míg az önmaguktól közlekedő kategóriába az AGV-k és a AMR-ek (autonomous mobile robot) sorolhatók. Ezeket a technológiákat anyagmozgatásra, raktározásra, illetve komissiózásra lehet használni, így automatizálva részben vagy teljes egészében a folyamatokat. De az automatizáció körébe tartozik az Ipar 4.0 is, amely szintén kihívást jelent az ipari szereplők számára, a fejlett digitális eszközök, szoftvermegoldások már ezen a téren is számos megoldást biztosítanak.
Ha már Ipar 4.0-s fejlesztések: milyen pozitív, kézzelfogható előnyei vannak a robotizációnak a raktárüzemeltetés terén?
Az automatizálás segít kiküszöbölni a szűk keresztmetszeteket, de további előnyei is vannak a raktári folyamatok optimalizálásán túl: a teljes vállalat versenyképességének növeléséhez hozzájárulhat. Milyen előnyökről beszélhetünk itt? Közép- és hosszútávon csökkennek az üzemeltetési költségek, a folyamatbiztonságnak köszönhetően a szolgáltatások minősége javul, minimalizálódnak a hibák, az átfutási idők rövidülnek, a munkatársak elégedettebbek, mivel csökken a fizikai leterheltség, a raktárban nagyobb a biztonság.
Ellenérvként szoktuk hallani, hogy a „gép” elveszi a munkát az embertől. Az automatizálás azonban azt jelenti, hogy csökken a dolgozók fizikai leterheltsége. Másképp kifejezve: javul az ergonómia, így csökken a testi panaszok száma és azok következménye. Ezzel párhuzamosan növekszik a biztonság, mivel a dolgozók kevesebb fizikai munkát végeznek, és ritkábban vesznek részt a raktárban folyó közlekedésben. Valójában egy automatizált raktár üzemeltetéséhez és karbantartásához is szükség van munkaerőre. Csak képzettebb vagy másképpen képzett munkaerőre.
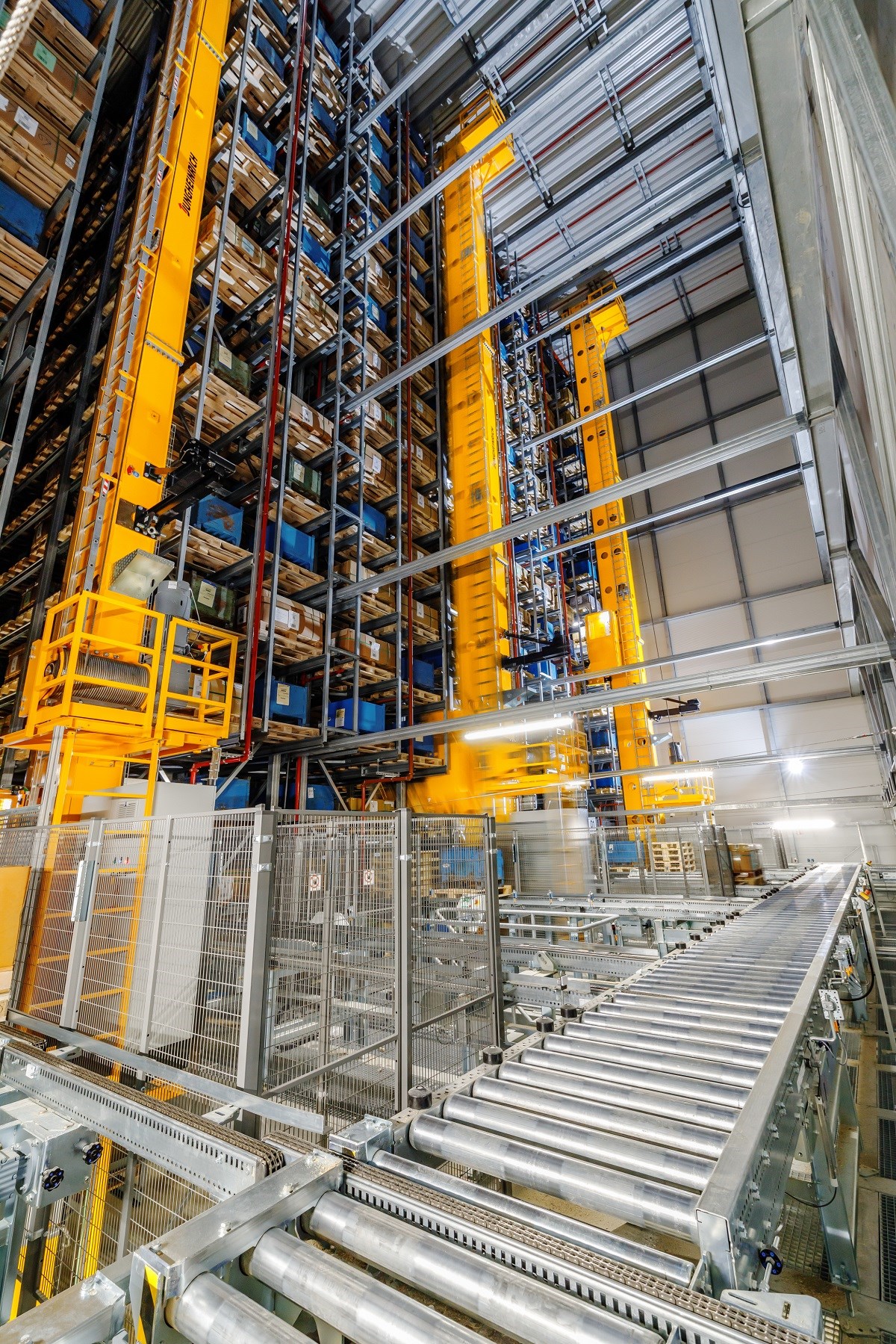
A robotizált folyamatok inkább javítják, semmint elveszik a munkát.
© Jungheinrich Hungária Kft.
Érdemes számos szempontot figyelembe venni a költségek esetében, hiszen automatizálással csökkenthető a ciklusidő, és akár két- vagy háromszoros kiszolgálási sebességgel lehet számolni. Az energetikai költségek is csökkenthetők, mivel az automata raktárak üzemeltetéséhez sem fűtésre, sem világításra nincs szükség – hacsak az ott kezelt termékek ezt nem igénylik –, és egy automata raktár napi 24 órában képes folyamatosan dolgozni. De az építési költségek tekintetében is kedvezőbb az automata raktár, hiszen kisebb területen lehet megoldani ugyanazokat a feladatokat, amit a manuális technológia esetében. A költségek vonatkozásában a beruházás mértéke az elején ugyan magasabb, de az automata raktár fenntartási költsége sokkal alacsonyabb, illetve az életciklus és biztonság tekintetében is hatékonyabb, mint a manuális megoldás.
A fent említettek alapján számos lehetőség rendelkezésre áll. Melyek a legfőbb szempontok, amelyeket mérlegelni kell egy vállalatnak, ha hatékonyabbá szeretné tenni raktárainak üzemeltetését?
Elsősorban a raktárban fellelhető problémás területeket, szűk keresztmetszeteket kell átvizsgálni. Hol láthatóak a napi működésben gyenge pontok? Van-e erre strukturális megoldás, vagy újra és újra ugyanazokkal a kihívásokkal kell megküzdeni? A szállítási és rakodási folyamatok automatizálásával erőforrásokat szabadíthatunk fel, optimalizálhatjuk az anyagmozgatást.
A szakemberek kiválasztásánál érdemes körültekintőnek lenne és olyanokra bízni a munkát, akik sok éve sikeresen működő projektekkel tudják alátámasztani alkalmasságukat. Mindig érdemes szem előtt tartani, hogy a zavartalan működtetés és karbantartás érdekében, már a tervezési fázisban olyan szolgáltatót válasszunk, aki mögött teljes körű szerviz és támogatási szolgáltatás, esetleg akár 0-24 órás készenlét biztosított.
Vannak-e nehézségek, elakadások a folyamat során? Partnerként a Jungheinrich ezeket hogyan tudja támogatni?
Az ügyfeleknek mindig egyedi igényeik vannak, mindenki szeretné a saját raktárára, üzemére szabott megoldást megvalósítani. Az esetek többségében erre találunk megoldást. Vállalatunk legnagyobb előnye, hogy teljes körű szolgáltatást nyújtunk, és ez szó szerint értendő: a termékektől a szolgáltatásokon keresztül egészen a gépek újrahasznosításáig szinte mindenre van megoldásunk. Ma már nehéz azt kijelenteni egy – egy termékre vagy szolgáltatásra, hogy egyedi. Rendkívül széles termékportfólióval rendelkezünk. A mi „egyediségünk” abban a leghangsúlyosabb, hogy ezt a nagyon széles termékpalettát kiemelt minőségben képviseljük és ehhez saját kézből teljeskörű after sales szolgáltatást biztosítunk. Úgy, hogy folyamatosan új, innovatív megoldásokat vezetünk be. Mind technológiai, mind szolgáltatási oldalon.
Milyen speciális egyedi megoldásokat kínálnak a raktárüzemeltetés terén?
Szeretnék kiemelni néhány úttötő projektet a hazai piacról: 2006-ban adtuk át az első automatizált magasraktárt az EGLO Magyarország Kft.-nél. Az első önvezető targoncát (AGV) 2015-ben helyeztük üzembe a Haribo Hungária Kft. gyárában. Az első önvezető szűkfolyosós targoncáink a FESTO-AM Pneumatika Gyártó Kft.-nél működnek, ahol egyébként számos automatizált rendszert fejlesztettünk és helyeztünk üzembe. A Jungheinrich tehát a targoncagyártó szerepet meghaladva már teljes körű intralogisztikai szolgáltatóvá vált, amely a tervezéstől a gyártáson át a megvalósításig egy kézből kínál mindent. Hagyományos, manuális állványrendszerek, félautomata és szinte teljesen automatizált megoldások mind a portfólió részét képezik.